稱取40g赤泥提鐵渣于三口燒瓶中,按照液固比5:1、6:1、7:1及8:1的比例加入鈦白副產酸,調整好攪拌轉速。在105 ℃條件下回流攪拌反應60 min,反應結束后,真空抽濾。再向濾液中投加一定量的氯酸鈉反應15 min,得到的PAFS檢測全鐵、氧化鋁、鹽基度的指標,檢測結果如下表:
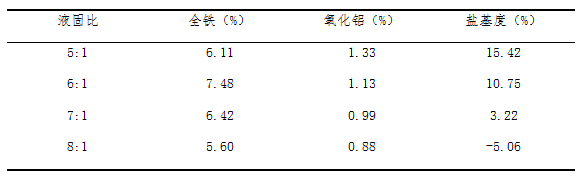
將濾渣烘干計算溶出率,實驗結果如下圖:
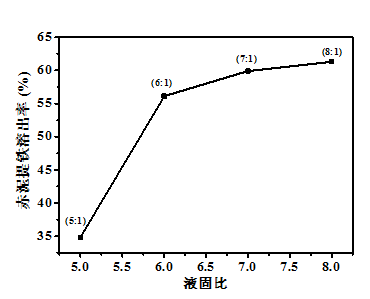
從上圖可知,隨著液固比的提高,一次溶出率值也越大。從5:1增加到6:1時其溶出率的增幅最大即由34.8%增加到56.1%,而當液固比高于6:1時,如果繼續增加液固比其赤泥溶出率變化幅度較小,在液固比為8:1時,赤泥提鐵渣的一次溶出率最大且高達61.3%。因為本反應為堿性氧化物與強酸的中和反應,體系中酸的濃度越高,越有利于赤泥提鐵渣的溶出。
從上表可以看出,制備得到的聚合硫酸鐵鋁產品因鈦白副產酸的過量投加會導致產品的鹽基度以及有效成分的含量下降,影響了產品的鹽基度指標和使用效果。綜合比較來看,在液固比為6:1時,赤泥提鐵渣的一次溶出率可以達到56.1%,制備得到的聚合硫酸鐵鋁有效成分含量最高,鹽基度也在理想的范圍內。同時未完全溶解的一次濾渣可以進行二次酸溶來提高赤泥提鐵渣的綜合溶出率。基于此,實驗表明最佳的液固比為6:1。
2、溶出溫度對溶出率的影響
稱取40 g赤泥提鐵渣于三口燒瓶中,按照液固比6:1的比例加入鈦白副產酸,調整好攪拌轉速。分別在95 ℃、100 ℃、105 ℃、110 ℃條件下回流攪拌反應60 min,反應結束后,真空抽濾。再向濾液中投加一定量的氯酸鈉反應15 min,得到的PAFS檢測全鐵、氧化鋁、鹽基度的指標,檢測結果如下表:
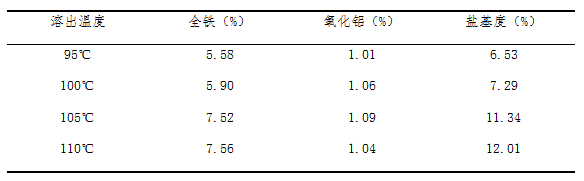
將濾渣烘干計算溶出率,實驗結果如下圖:
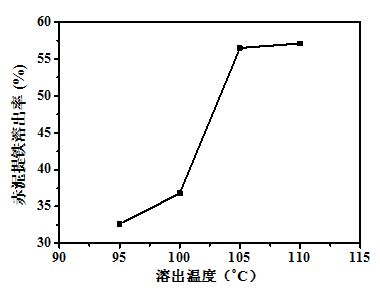
溶出時間對氧化鋁的溶出率影響較小,對氧化鐵的影響比較明顯,這是因為鋁離子的反應活化能較鐵離子反應活化能要更低。從上圖可知,聚合硫酸鐵鋁溶出率隨著溶出時間的增加而調高,80 min時溶出率高達65.2%。繼續延長到100 min時溶出率最大,達到了66.0%,與80 min相比較溶出率變化不大。但過長的溶出時間也意味著過高的能耗,基于此,最佳的溶出時間為80 min時,即溶出率為65.2%。
相關文章:-------------聚合硫酸鐵鋁與市售混凝劑處理效果對比